The Inspection, Cleaning, And Testing Of Composite Hose
INSPECTION
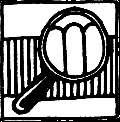
Worn or damaged hoses may be dangerous, therefore, hoses should be visually checked before each operation and given a more rigorous examination at least every 6 months.
The inspection should pay attention to:
- Dents to kinks.
- Displacement of inner and outer reinforcing wires from their normal pitch.
- Corrosion or abrasion of the outer wire.
- Displacement of end fittings or signs of leakage from the ends.
- Other abnormal features including wear or damage to end fittings.
- Chemical attack, deterioration or physical damage to outer cover and carcass generally.
Hoses with any significant defects of the above type should be retired from service. Moderate abrasion of the outer covers acceptable if the reinforcing fabric below the cover is undamaged.
CLEANING
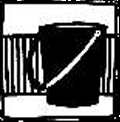
Hoses should be cleaned after use and always before testing or prolonged storage. The most appropriate method will depend on the hose use and its location.
Flushing out is often sufficient, with fluids such as: clean water, hot water, detergents, common solvents at ambient temperatures, sea-water. If sea-water is used, it must be thoroughly drained afterwards to minimize risk of corrosion on Carbon steel end fittings or Galvanised steel interval wires.
It is essential that any strong acid conveyance is thoroughly drained prior to cleaning, to avoid exothermic reaction. It is also important to fully drain the hose afterwards to ensure puddles of cleaning fluids are not left within the assembly. This avoids any possibility of chemical reaction when the hose re-enters service
Loose steam may be used but the hose must be open-ended and then its maximum working temperature must not be exceeded since damaged to the fabric or film may occur. Compressed air may be used, but again the hose must be open-ended.
During cleaning the hose must be electrically earthed to avoid static charge build-up, especially near flammable areas.
Pigging must not be used any circumstances.
TESTING
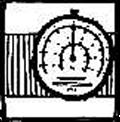
At least annually, hoses should be hydraulically tested as follows:
- Drain and thoroughly clean hose, and check end-to-end electrical continuity.
- Inspect visually. Hoses failing visual inspection should be not tested.
- Lay the hose straight out on supports or roller bed that allows free movement under pressure.
- Blank off ends and fill the hose completely with water. Ensure trapped air is released by tilling slightly.
- Pressure the assembly to 1.5 times the maximum rated working pressure and hold at this pressure for 10 minutes while examining for leaks. Also test electrical continuity between ends to ensure that it’s the same as initially checked.
- Release pressure and drain hose.
- On completion of the test, the hose should again be tested for electrical continuity.
It should be noted that with thermoplastic composite hoses, elongation under pressure can be high relative to rubber. This is a feature of composite hoses and unlike rubber hoses, it cannot to be taken as an indication of failure or used to assess the condition of the hose reinforcements.
ELECTRICAL CONTINUITY TESTS
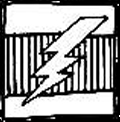
To prevent the accumulation of static charge generated in use, all metal parts of the assembly have been electrically bonded during manufacturers. At intervals not exceeding 6 months, the following tests should be carried out.
- Lay hose flat on the ground.
- Check that it is electrically continuous end-to-end with approved electrical measuring device.
Hoses not having electrical continuity should be retire from service.